5 Ops Down To 2 Brings Big Savings To Subcontract Valve Machining
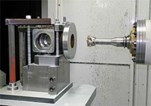
Warwickshire, UK - A Japanese-built, 4-axis, horizontal machining center from OKK, delivered by UK agent Whitehouse Machine Tools in January 2007 to subcontractor Clanalvex Precision Engineering, is able to perform nearly all machining operations on valve bodies in one CNC cycle. The only second operation, carried out on a modified center lathe, is back boring of an internal seat pocket. Clanalvex is working on including even this into the cycle so that valves can come off fully machined.
This is in stark contrast to the previous production route, which required five set-ups on different machine tools. Flanges had to be rough-turned on a center lathe, after which the forging or casting was transferred to a 4-axis vertical machining center (VMC) for machining of the port. A further turning operation followed to finish-machine the flanges accurately relative to the port. The fourth operation was either machining of the seat pocket on the modified lathe or conventional drilling of an angled hole in the bore, followed by drilling of holes in the flanges on another VMC.
Compressing most of these operations onto the OKK HM400 2xAPC horizontal machining center (HMC) has cut at least 30 per cent out of the metalcutting cycles alone, thanks to acceleration at 0.6g to 54 m/min in each orthogonal axis, 90-degree rotation of the table in half a second, and 1.2 seconds tool-to-tool change. In addition, a lot of time is saved and accuracy preserved by not having to transport work-in-progress between machines and repeatedly reclamp the valves.
Commented Steve Scott, Sales Director of Clanalvex, "One of the biggest drawbacks with our old method of valve manufacture was that we kept running out of tools in the carousel of our VMC, which forced us into multiple set-ups and consequently increased machine down-time.
"Another problem was that the 4th-axis indexing tables on our VMCs were not really strong enough for port machining, causing inconsistency in our finished product. We were for ever chasing the required tolerances of less than ± 30 microns."
Consequently, at the top of Mr. Scott's shopping list when the decision was taken to invest in a new machining center were rigid construction and a large tool magazine.
Both he and production director, Kevin Wallace, also favored a horizontal-spindle machine to allow all-round access to a valve so that it could be machined in one operation on a robust rotary table. They were not deterred by HMCs normally being regarded as high production machines, even though batch sizes for this machine at Clanalvex rarely exceed 30-off and frequently drop to ones and twos if, for example, a power station valve fails and needs urgent replacement.
There are hundreds of variations to any one of the standard product families, so the twin pallet changer was seen as providing a way of minimizing non-cutting time by allowing the next component to be fixtured while the previous one is being machined.
The biggest advantage, however, was being able to have jigs set up for completely different components, allowing the flexibility of being able to produce two batches of work concurrently and economically on the two pallets.
"I have bought many machine tools in my professional career and hold the view that, overall, you get what you pay for," commented Mr. Scott. "In the case of the OKK, we felt we got excellent value for money."
"Our customers are looking for superior quality and faster delivery compared with even a couple of years ago, so a machine tool must be both accurate and reliable, and the agent must be able to demonstrate a high level of service back-up."
He explained that three of the best-known suppliers in the industry were approached in addition to Whitehouse. Details of the four shortlisted HMCs were evaluated with the help of a spreadsheet and, whilst the others showed themselves to be of top quality, the OKK was the clear leader for the intended application at Clanalvex. In addition, the specification of the model in the showroom was almost ideal, with its 40-taper BIG Plus spindle, 60-position tool magazine rather than the standard 40-tool version, and 70-bar through-tool coolant.
A professional demonstration at Whitehouse's showroom in Kenilworth, and an agreement that the agent would guarantee next-day delivery of a replacement spindle should that ever prove necessary, clinched the deal.
Clanalvex, now in its third generation of management following a buy-out in 2003 involving Mr. Scott and three other directors, has been located on the site of a former railway station goods yard (courtesy of Dr. Beeching) for nearly 45 years in a little village eight miles south-west of Scarborough. Called Brompton-by-Sawdon, it has a population of 516 and was the focus of much curiosity when the HM400 arrived just after New Year on two articulated lorries.
The machine has worked without incident since it was levelled, plugged in and commissioned. Just two weeks after installation, an order came in at 4.00 pm for two valves to be machined urgently. Admittedly Clanalvex had been given a few hours' advance warning, so the core program had already been transferred across from a VMC and edited, and the jig was on the HM400 waiting for the material to arrive.
Nevertheless, completion of the two valves by 7.00 pm, allowing them to be shipped back to the customer that same evening, without stripping out the job that was already on the machine, was testament to how quickly the OKK took its place alongside the other nine CNC machines on the shop floor at Brompton.
SOURCE: Whitehouse Machine Tools Ltd.