Case Study: Conicity Gives Accurounds A Significant "Edge" In It's Machining Operations
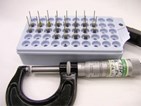
There are very few companies for whom "too good" is actually not good enough. AccuRounds happens to be one of them.
This doesn't apply to the products the company fabricates for its customers. Located in Avon, Massachusetts, AccuRounds manufactures precision custom cylindrical components of all types and sizes for customers and OEMs in a wide spectrum of industries. These components range from miniature heat-treated pins for the bearing industry to large drive shafts for paper feeding machines. Machined from a multitude of materials such as stainless and carbon steels, titanium, aluminum, plastic and a variety of alloys and exotics, the components that AccuRounds produces have gained a reputation for quality that is second to none.
No, the "too good" dilemma applies to the machines that AccuRounds uses to manufacture these components.
"Even though we use sharp tools, they can actually be too sharp," explained Mike McCormick, AccuRounds's engineering manager. "Sometimes, we have a tool like a drill bit that had just been sharpened; it has a sharp edge, and a sharp edge does not always exhibit good metalcutting characteristics."
"When we would first mount the drill bit, we'd get quite a bit of chatter, resulting in tearing and finish problems on the metal or even damaging the grain. Certainly, not every job involves a part that requires a very smooth, perfect finish, but for those parts that do, this became problematic."
This quandary was not solely indigenous to AccuRounds. It is, in fact, representative of a larger issue: the issue of tool edge preparation. In recent years, tool edge preparation has been universally recognized as one of the four main ingredients required in successful cutting tool manufacturing. These ingredients include:
- Tool substrate composition (tool base material)
- Tool geometry
- Proper coating (if required)
- Edge preparation
R&D efforts over the past two decades have focused primarily on the first three, with vast resources being expended in these areas to develop more reliable and repeatable processes. In comparison, the fourth ingredient, tool edge preparation, has been largely neglected. One would suppose that the negative ramifications of poor tool edge preparation would have catalyzed more technological development in this area, yet this has been far from the case.
Conicity Technologies has carved a sizable market niche by focusing attention on the fourth ingredient, earning a reputation as the leader in cutting tool edge preparation technology. In fact, Conicity was founded specifically to develop and market a new generation of cutting tool honing systems, which allow both the tool manufacturer and the end user to achieve optimum performance for each application.
Conicity's systems are designed to apply the correct micro-geometry to a tool's cutting edge based upon the specific requirements of the application, whether it is a manufacturer's generic line of tooling or an end-user's specific operation. The system employed by Conicity is Engineered Micro-Geometry™. This system provides the ability to apply the proper geometric shaped edge prep and precisely distribute that edge prep on the cutting edge of a tool as a function of the thickness of the uncut chip. Essentially, this means that, rather than preparing the edge in a conventional and uniform manner, the cutting edge is prepped in a fashion that is unique to how the tool is going to be applied to the work piece material in the given operation. This type of controlled edge geometry is the key to optimizing the performance of any tool resulting in maximum tool life, superior surface finish and flatness, and minimization if not elimination of burr formation.
AccuRounds has used Conicity's edge preparation services to great advantage.
"Our customers are quite serious about the finish on their parts," said McCormick. "In many cases, they insist that there are no scratches or chatter marks, and the finish has to be very smooth. Conicity's edge prep service gives our tools an incredibly stable cutting edge while allowing us to provide our customers with the finish they are looking for."
The precision behind Conicity's EMG process is particularly impressive given the fact that AccuRounds is sending out tools that sometimes have a diameter down to as little as .0025 inches, which is very small considering the human hair is only .004 inches. "And they are working only with the edge," McCormick noted. "The narrow band of contact between the tool and the workpiece is a pretty small area." Actually, it is microscopic in size.
AccuRounds's positive experience with Conicity is clearly illustrated by an edge prep test that Conicity recently completed.
"When we met [Conicity Executive Vice President] Bill Shaffer at IMTS [the International Manufacturing Technology Show], we told him that we were forming a special shape with a carbide form reamer into 316 stainless steel," McCormick recalled. "The results were outstanding, but we were having trouble every time we set a new tool into place – lots of chatter, tearing and finish problems, the works. Plus, we always ended up with a huge pile of scrap pieces before the tool finally wore in properly."
The test was performed without changing any other aspects of the process, i.e., same machine type, feeds, speeds, removal amounts, material, cutting oil, etc. According to McCormick, with the Conicity edge prep used on tools from the same batch, AccuRounds was able to produce parts with acceptable finishes immediately upon part change. Problem solved.
While providing customers with parts that exhibit a superior finish is the primary objective, the edge prep services have helped AccuRounds realize some unexpected results.
"The bonus we discovered after the fact was that the prepped tool lasted close to 10,000 parts," said McCormick. "Prior to the edge prep, the tool life was around 1700-2000 pieces before the finish degraded beyond the point of acceptability. Apparently, the properly edge prepped cutting edge allows for more even tool wear, which helps maintain the desired finish much longer."
AccuRounds has also seen substantial timesavings as a direct result of the Conicity process. To begin with, there is no longer a tool "breaking in" period, during which the large volume of scrap pieces is generated. What's more, the increased tool life means that fewer part changes are necessary. While each tool change may not involve a vast amount of time, the total timesavings from eliminating multiple part changes becomes significant. This also translates to faster turnaround times and, ultimately, faster product delivery times.
Given the benefits of EMG, it's a pity that a greater percentage of AccuRounds's tools are not candidates for this process. McCormick estimates that only about 10% of all the company's tooling currently requires edge preparation. However that percentage is growing almost daily.
"Because our clients' manufacturing needs are so diverse, the opportunity to use off-the-shelf tooling is becoming increasingly infrequent," McCormick said. "And the more custom tooling we produce, the greater the need for Conicity's edge preparation services.
"In fact, I've got about 20 or 30 new tools right now that we're getting ready to send over."
As pleased as AccuRounds is with Conicity, it's the end-user customers whose feedback matter most.
"We have had extremely positive feedback from out customers on the improved quality of the parts we're producing," said McCormick. "They're quite pleased. The bottom line is that we're giving them perfect pieces and we're getting them out faster.
It appears that Conicity has done more than put precise edge prep on AccuRounds tooling. The company has also helped give AccuRounds an edge in the marketplace.
SOURCE: Conicity Technologies, LLC