Case Study: Curtis-Toledo Integrates Rotary Screw Compressor Line with High Performance Drive and Software for Energy Savings
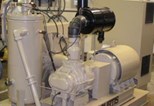
Full Study: Curtis-Toledo Integrates Rotary Screw Compressor Line with High Performance Drive and Software for Energy Savings
When Curtis-Toledo, Inc. was looking for an innovative way to make its rotary screw compressors more energy efficient and operator-friendly, they turned to local factory support from ABB Inc., Low-Voltage Drives. Along with supplying drives to control speed and torque of the compressors, the ABB project team designed software to control the screw compressor's system pressure, air delivery, oil temperature and duty cycle directly from the drive, eliminating the need for an additional external controller.
Optimizing the Fourth Utility
Curtis-Toledo's 5-300 horsepower screw compressors are used to power equipment and operations in a variety of applications and industries. Compressors are a plant's "fourth utility," providing the air that is crucial to operating many of the pneumatic tools and machines. While many industries still operate these compressors in standard fixed-speed mode, energy costs are prompting others to retrofit their compressors with adjustable-speed drives in order to provide and control air-flow supplies in direct response and proportion to real-time operating (load) conditions. (By precisely matching the compressor output flow and pressure to the actual, instantaneous demand of the customer's process, the compressor operates at its' absolute best efficiency.)
Eliminate Separate Control Device!
Currently, virtually all compressor manufacturers use either a standard PLC logic controller or a custom designed OEM, board-level controller; either way, the control logic of the machine is handled via a separate device. ABB's innovative approach is to eliminate these separate controllers (and the expense associated with them), and use the processing power of the ABB ACS800 drive, to not only control the motor, but control the entire compressor, as well. This approach makes the ABB concept more reliable than competitive designs because a major component (PLC or board-level controller) is eliminated. This also lowers the cost of the variable speed solution.
A unique feature of the ACS800 drive is the ability of the drive to perform the basic function of controlling the speed of the motor and, at the same time, use it's processing power and extensive I/O to act like a traditional PLC (programmable logic controller).
The standard ACS800 drive includes a set of application function blocks – data blocks that can be programmed to perform any operation from a predefined set of functions. These function blocks give the drive it's PLC functionality. The function block programming allowed the ABB project team to use the drive to control the entire machine. This combined drive capability makes the Curtis Toledo AF Series Compressor the cleanest, most efficient design in the industry.
Due to the complexity of controlling a screw compressor in the most efficient way possible, ABB decided to go a step further by completely customizing the drive firmware to optimize the control system. Again, ABB's solution has eliminated the need for either a standard PLC or a proprietary board level controller.
"We've enhanced the capability of the drive without the cost and inconvenience of add-ons such as PLCs, which require external mounting, wiring and added space," says Steve Boren, the ABB application engineer who customized the software for Curtis-Toledo's machines. "Typically, air compressors operate at fixed speeds and, when operating at partial loads, they are expending unneeded energy. With a drive built into the compressor as an integral part of the machine, compressors operate at greater efficiencies – including matching air volume to demand; providing energy savings as the variable speed slows the motor down when air demand decreases; and audible noise reduction because, at lower speeds, compressors generate significantly less audible levels than at full speeds."
Through the software, the drive regulates and changes speed to match the exact air demands from the plant or facility. The compressor does not load and unload because that wastes energy. Air is only compressed once -- and only in the volume needed to meet the demands of the system.
"Having a variable speed drive (VSD) integrated into our compressors is precipitated by industry demand," says Jerry Elson, national sales manager for Curtis-Toledo. "VSDs are coming into play where energy costs are higher, such as in California or the Northeast. And demand is getting stronger. With the ABB drive and software, we feel that Curtis-Toledo is ahead of the curve." The ABB drive software includes a formula that continuously calculates the energy savings, so the end user can see the dollar savings on demand by viewing a touch screen.
"This whole application is about saving energy, so having a touch screen that displays the calculated energy savings as the machine is running is the biggest benefit, followed by its ability to monitor the working conditions of the compressor," Elson says.
Click Here To Download:
Full Study: Curtis-Toledo Integrates Rotary Screw Compressor Line with High Performance Drive and Software for Energy Savings
SOURCE: ABB Inc.