Design Maximizes Floating Holder Benefits, Minimizes Drawbacks
Machine tool builders and users continue to search for ways to eliminate problems commonly associated with high-production tapping and reaming operations. These problems include reduced tool life, poor surface finish, faulty thread sizes, and oversized holes. Introduction in the 1970s, the floating holder concept helped eliminate some of these trouble spots. But some of the same errors also continued to exist in leading floating designs.
Until now, that is. T.M. Smith Tool International (Mt. Clemens, MI) says its coolant-thru DuraFloat floating holders feature an anti-friction parallel floating drive that results in reliable tool performance and extended tool life. More important, the company says, the tools are among the only ones on the market that provide 0.062 to 0.094 in. of radial float without the use of balls or rollers.
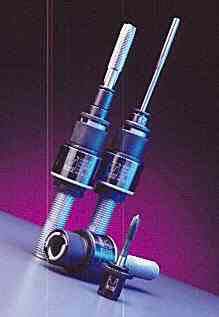
New Variation on Oldham Theme
T.M. Smith says most floating holders, whether they feature a roller or rollerless design, use one of two variations of the Oldham coupling design to transfer radial driving forces from the shank to the floating nosepiece. One variation uses two pairs of driving pins, located parallel to the tool axis and at 90 deg to one another. This method allows for short overall length but results in large, cumbersome outside diameters.
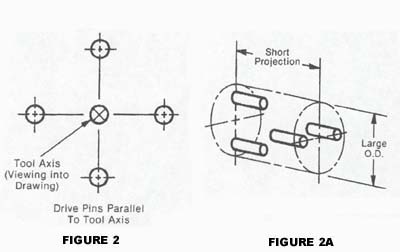
The second method also features two pairs of driving pins, but the pins are located perpendicular to the tool axis. This variation produces small outside diameters, but at the expense of increased tool length.
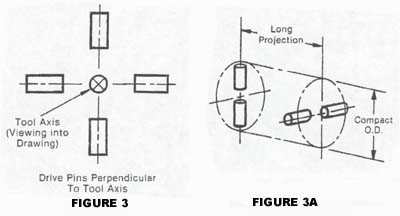
To solve these problems, the DuraFloat holder combines the two Oldham Coupling designs. The shank pair of driving pins are parallel to the tool axis while the nosepiece pair are perpendicular to it. The resulting floating holder features both a short overall length and a small body diameter. With this design, DuraFloat has the ability to drive both large and small taps and reamers.
Instead of depending upon small contact areas like those commonly associated with balls or rollers, DuraFloat's anti-friction parallel drive uses large surface areas treated with wear-resistant coatings. This process hardens the floating member surfaces, increasing wear resistance while reducing friction. The coating is also optional on all remaining component surfaces for additional rust and corrosion prevention.
Serious Wear Flaws Avoided
Eliminating balls and rollers does more than increase DuraFloat's reliability. The balls and rollers of other floating holders work in a back and forth motion in a very small area causing small depressions to form in the floating member surfaces. When this happens, radial and axial looseness develops, causing many common floating holder problems including tool chatter, bell-mouthed holes, and poor holder life. With DuraFloat holders that feature only two moving parts, these problems have been effectively eliminated.
In addition, most floating tap and reamer holders fail to effectively seal the floating mechanisms from contaminants such as grease, dirt, coolant, chips, and grime. To combat this problem, DuraFloat utilizes a Teflon-molded seal that exerts constant force against the ground front face of the housing while the Teflon's lubricating characteristics offer a minimum resistance to motion.
High-pressure Coolant
DuraFloat is capable of providing coolant-thru the holder at up to 1000 psi, and in some cases, higher. The centering toolholder mechanism design allows the inlet flow to be controlled, reducing pressure on the mechanism, and allowing higher coolant pressure to be used.
The design also is ideal for use with rotary coolant inducers. These attachments are typically used with older equipment when coolant-thru spindles are not available. With most other floating holder designs, the inducer is attached to the nosepiece of the holder, creating an undesirable size and weight condition that doesn't permit the holder to float true. With DuraFloat, the rotary inducer can be placed behind the centering mechanism allowing the coolant to flow through the holder with true float.
Heavy drive pins give DuraFloat holders the ability to transmit more torque to the tool through the floating mechanism. This design also allows the body diameter and length to be used in tight, multiple spindle applications.
Through the use of interchangeable components, DuraFloat is available in a wide variety of models and sizes to satisfy a complete range of user needs. This multitude of configurations contains all popular Morse Taper, straight, automotive, and metric shanks, as well as collet and quick-change tap adapter nosepieces.
T.M. Smith Tool International, 360 Hubbard Ave, Mt. Clemens, MI 48046. Phone (810) 468-1465.