Shrink-Fit Toolholders Just the Ticket for High-Speed Machining
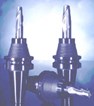
As spindle speeds, machine feeds, and accuracy demands increase, toolholders are in danger becoming the weak link in the metalcutting chain.
Set screw and collet chuck toolholders—still the most popular types—inherently limit spindle speed and precision. Hydraulic holders and milling chucks allow for faster and more precise machining, but they are more expensive, relatively bulky, contain moving parts, and complicate coolant delivery to the cutting area.
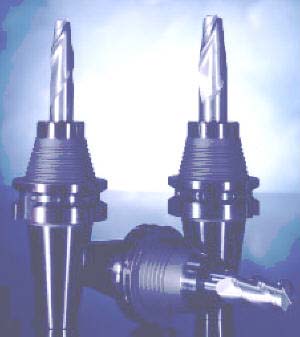
Enter shrink-fit toolholding. Superlatives abound in descriptions of the technology: most gripping strength, highest machining accuracy, lowest possible total indicator reading (TIR), and best possible inherent balance are just a few. Shrink-fit tooling effectively becomes an integral shank tool, virtually eliminating tool deflection, vibration and slippage.
How It Works
The shrink-fit concept is simple. Toolholders are manufactured with an ID slightly smaller than the cutting tool shank diameter. Heat—produced by one of several methods, including induction heating and hot air—is used to quickly expand the toolholder ID, allowing the tool shank to slip easily into the holder. As the holder cools, the resulting contraction exerts a very high uniform pressure around the entire surface of the tool shank.
Removing the tool is as simple as reversing the process. Tool changes can be accomplished very quickly, increasing productivity by reducing tool change downtime.
The system provides total concentricity, according to one supplier. That means machining accuracy depends only on the machine tool and cutting tool tolerances. Total concentricity also reduces tool and machine wear, runout, and scrap. And, shrink-fit systems can deliver coolant right through the toolholder if needed.
How to Heat It?
Suppliers of shrink-fit tooling may be in unanimous agreement on the system's metalcutting benefits, but that isn't stopping them from offering an array of systems for heating the toolholder for tool insertion and removal.
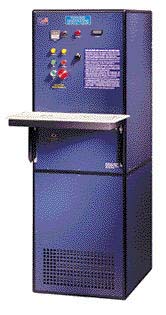
Propane gas heating is the most basic method available. More common is induction heating, which is fast and relatively simple. According to one supplier, an average induction cycle takes 7 sec to expand the toolholder ID enough to allow the operator to change tools. The ID shrinks back only a few seconds after tool insertion, and the tool is ten placed in a cooling block to speed cooling. The entire procedure takes less than 30 sec.
Another approach to expanding the holder ID is to use hot air. Proponents of this system say using hot air inputs the minimum amount of heat needed to expand the toolholder body, improving safety and reducing cooling time.
One system uses dual 4,000-W heaters to expand the toolholder ID. Although the system may take longer than induction units to heat the tool, total tool change time is said to be comparable because temperatures are held to the minimum necessary to expand the holder.
The same supplier also offers infrared heating, which it says is appropriate for users who perform frequent tool changeovers.
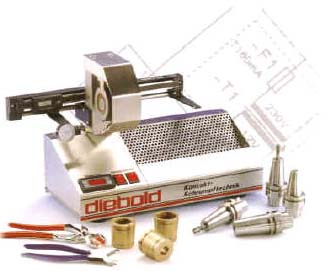
Then there's "contact-shrink," which the supplier says offers multiple advantages over other approaches, including:
Shorter cycle time
Less cool-down time
Localization of heat where it's needed to eliminate taper potential taper distortion
Low energy consumption and noise level
Low cost
The contact system currently is available for BT40, BT50, and HSK shanks; other systems are applicable to all standard BT and CT toolholders and HSK shanks.
The Safety Factor
Regardless of approach, the heating system must expand the toolholder enough to allow tool insertion and removal without overheating, which can shorten holder life.
Besides, the dangers involved in having a human handle a hot toolholder in one hand and a sharp cutter in the other should be obvious. Most systems eliminate manual tool installation both to improve safety and to maximize system efficiency.
One supplier, for example, uses a fixture mechanism to provide hands-off pressure on the cutter to allow insertion at the lowest possible temperature. Tools are held vertically, pointing either up or down depending on whether they're being inserted or removed, to take advantage of gravity.
Proponents of horizontal systems say their approach provides better access to adjustment bolts than vertical systems. One horizontal system comes with an integral tool presetter that lets users quickly set tool length using a dial indicator gage.
Diebold Goldring Tooling U.S.A., 206 Baldwin St., Box 501, Sharon, WI 53585. Phone (414) 736-2204.
Lyndex Corp., 3160 Commercial Ave., Northbrook, IL 60062. Phone (800) 543-6237.
Production Dynamics, 2351 Industrial Dr., Valparaiso, IN 46383-9511. Phone (800) 445-1196.