When the Cutting's Over, Service Can Help Managing Waste Coolant Economically
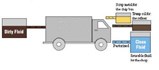
Metalworking fluids cost money--purchasing new quantities, cleaning, and safely disposing of them at the end of their useful life.
Some shops have bought equipment and assigned personnel to clean machine sumps and replenish fluids. It is an unpleasant, costly task, especially for shops using 1000 gal or more a month. Worse, it is peripheral to the real business of making parts.
A more cost-effective route can be to hire a certified environmental services company to manage and recycle your metalworking fluids. The approach has several advantages over DIY coolant management: there's no equipment to buy, shop personnel are not used for nonproductive tasks, and disposal problems are avoided.
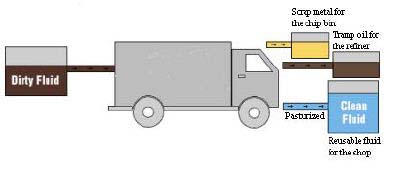
Do the Math
Coolant disposal costs charged by a licensed waste hauler range from $0.10/gal to $0.90/gal, depending on location, competition, and state and federal regulations. Disposal fees can also include hidden costs such as labor charges, transportation fees, and demurrage charges.
Whenever you dispose of a gallon of coolant, you must replace it with new pre-mix coolant. Replacement costs--the largest part of coolant disposal cost--can range from $0.20/gal to $1.20/gal. Cost depends on coolant cost per gallon and concentration.
To check your potential savings from coolant recycling:
1) Multiply your coolant cost/gal by target coolant concentration to get coolant replacement cost/gal.
2) Add coolant disposal cost/gal to get total coolant replacement and disposal cost.
According to John Coyle, account manager at Fluid Recycling Services (FRS; Livonia, MI), using an outside coolant management service can result in substantial savings versus DIY. "Fluid Recycling Services has saved its customers from $4,000 to $100,000 a year, depending on how much fluid is recycled, compared to the cost of their doing it themselves" he says.
How Mobile Recycling Works
FRS customers get holding tanks ranging from 1000 to 3000 gal for dirty and clean coolant. Shops place coolant from sump changes, skimming, and other sources into the dirty tank. The used coolant is contaminated with tramp oils, chips and fines, and bacteria.
FRS regularly--typically monthly--visits the plant with its mobile recycling unit. The dirty coolant is pumped through the mobile unit, where the coolant is cleaned and made ready for reuse.
The unit first removes heavy tramp oils and smaller contaminants. The fluid is heated to remove bacteria and mold, then passed through a centrifuge to remove any remaining tramp oil and fines. After cooling, the recycler check the fluid for purity and routes to the clean tank when acceptable. Finally, the coolant is tested against predetermined standards, and the recycler makes any needed adjustments.
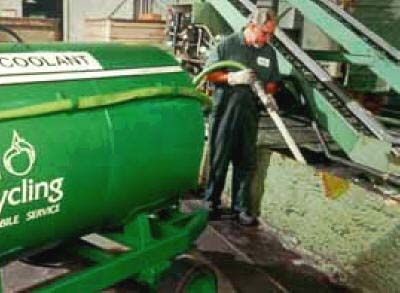
After recycling, the user has clean, fully effective fluid, treated with biocide and appropriate additives, and receives a fluid analysis. Users report significantly lower coolant replacement costs--up to 70% in some cases--and reduced disposal costs, plus the added benefits of greatly reduced environmental risks and maintenance costs.
Kick It up a Notch
Mobile recycling is one of the services offered by FRS. The company also has sump changing and machine cleaning services that can be performed regularly or during shutdowns. FRS says regular sump cleaning results in improved machine performance, longer tool life, and reduced machine downtime.
And large plants may opt to have FRS personnel and equipment on-site for total fluid management, which includes machine coolant control and maintenance, sump-changing, machine cleaning, top-off, and fluid recycling.
Besides immediate costs savings in terms of reduced labor, coolant disposal, and reduced chemical usage, users report improved plant environment and reduced environmental liabilities. Plant personnel can focus on the core business of manufacturing and machining, permitting increased plant productivity. And, the cost of fluid management can be identified and fixed for a defined term, resulting in improved accounting and having a positive effect on cash flow.
Fluid Recycling Services, 31690 Glendale, Livonia, MI 48150. Phone (800) 358-4374.