Subcontractor Diversifies Into Mold Making With 5-Axis Machining Center
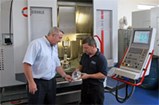
UK - In February 2007, Gosport-based subcontractor Norjon Engineers doubled its annual turnover to more than £1 million by acquiring the order book of a local business specializing in thermoforming molds for the food industry. Owner and managing director, Kevin Fox, decided to invest in new machine tools to produce the aluminium molds. He wanted to improve their quality and deliver them faster to manufacturers of thermoformed plastic packaging such as yogurt pots, trays and disposable cups.
For this new side to the business, in addition to a 10-inch chuck lathe to make rotational parts, Norjon needed a 5-axis machining center, plus CAD/CAM software to handle customers' data and generate programs. From a shortlist of three machining centers, the decision was taken to invest in a Hermle C 20 U from UK agent, Geo Kingsbury Machine Tools, despite the machine being a little more expensive than the others.
"We have been blown away with the quality," enthused Mr. Fox. "Surface finish is important on our molds, as good cosmetic appearance is a prerequisite for plastic packaging in the consumer industry. The finish off the Hermle is of such high quality that we do not have to hand-polish molds after machining."
To maintain continuity of mould supply to established customers, Norjon needed to re-equip quickly. The C 20 U was delivered on a Monday morning towards the end of April 2007 and was commissioned and cutting metal by the next afternoon. As a temporary measure between February and April, Mr. Fox was able to produce moulds using a similar Hermle machine in Geo Kingsbury's showroom, also located in Gosport.
Paul Dodman, who has 20 years' experience in the thermoforming industry, was recruited by Norjon from the moldmaking firm that closed. He said that there is no comparison with the old plant he used before. He is particularly impressed with the compactness of the Hermle and its build quality, from the stainless steel-lined working area down to cabinet for the cooling unit.
Rapids of 54 m/min and a 16,000 rpm spindle make for fast cycle times, while the robust rotary table and trunnion arrangement with its bearings set directly into the mineral casting that forms the bed ensures that ± 20 microns tolerance can be easily held during full 5-axis machining of deep features with steep draught angles.
Even though the factory is on single-shift working, there is spare capacity on the C 20 U to manufacture components other than molds. Norjon has already moved some prismatic machining across from its 3-axis equipment to take advantage of more efficient production in fewer set-ups that result from automatically positioning and clamping the extra two axes.
The company is looking to take on additional work that is suited to the machine's capabilities, including other types of molds and tools except plastic injection molds. With the aid of its Delcam software, it is able to import customers' data in most formats, provide a design service where required and program complex, 3-, 4- and 5-axis cutting cycles.
Now the second largest machine shop in the area, Norjon is a good example of how to succeed in subcontracting at a time when many have been going out of business. Founded in 1984 by Norman Goff and John Aslett with a manual lathe and mill in a Fareham garage, the company was bought by Kevin Fox in 2002, financed by remortgaging his house and a five-year bank loan.
At that time the shop was still full of manually operated lathes, mills and grinders. Since then, Mr. Fox has invested in modern CNC plant and inspection equipment, purchased the mouldmaking concern and moved twice to progressively larger premises, all at a cost of more than £500,000.
There is often a seminal moment in the success of a business and in Norjon's case, it may well have been the decision by Mr. Fox to branch out into gearcutting for the printing industry in the middle of a downturn during the fourth quarter of 2004. He bought two machines and employed an extra operator to fulfil a contract. The contribution to turnover was important at a time when other metalcutting work was scarce. The gearcutting side of the business has since grown, with four machines in regular operation.
SOURCE: Norjon Engineers