Tyrolit Launches Two New Ranges Of CBN Grinding Wheels
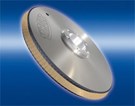
Schwaz, Austria - Two new ranges of external cylindrical grinding wheels, one using cubic boron nitride (CBN) grains in an electroplated nickel matrix and the other based on CBN grains in a vitrified bond, have been introduced by Tyrolit. Called POLARIS and GENIS respectively, they are intended for large volume production of components from difficult materials such as hardened steel and tough exotic alloys.
Compared with competitive CBN wheels, increases of up to 60 percent in wheel life are claimed for the new superabrasive products. They are aimed mainly at the automotive sector, although applications are to be found in the aerospace, motorsport, medical and bearing industries as well.
More aggressive grinding and hence shorter cycle times are achieved with CBN compared with aluminium oxide wheels, leading to higher productivity and lower cost per part, assisted further by fewer wheel changes, lower infeed force and energy consumption, and reduced machine wear.
Contributing further to economical manufacture of components is less frequent truing and dressing of the vitreous bond CBN wheels, while the single-layer electroplated types do not need to be dressed at all. Tighter dimensional tolerance, better surface finish and improved metallurgical integrity of the manufactured components leads to improved repeatability of the grinding process.
Sharpness, thermal stability and high fracture strength of Tyrolit's CBN crystals are at the heart of the high grinding ratios achievable with POLARIS electroplated and GENIS vitrified wheels. For each application, Tyrolit analyses and optimizes the process, providing a turnkey package including a tailor-made wheel for the application and the machine on which the components will be ground, and advice on wheel preparation, grinding parameters and coolant delivery.
The strong, laminar structure of the nickel layer securing the CBN grain in POLARIS wheels, together with the grain's free-cutting topography, allow previously unattainable adhesion strength to be achieved for external grinding. Wheels up to 700 mm in diameter and 450 mm wide can be supplied to a maximum wheel weight of 150 kg. Run-out, concentricity, parallelism and right angularity are all accurate to within 5 microns.
In one test application for a customer, involving roughing the cam profile and bearing journals of a cast iron camshaft on a Schaudt CF41, a 404 mm diameter wheel using a new grain quality and embedding depth, running at 120 m/s, increased tool life from 85,000 to 130,000 parts.
A second success was achieved grinding turned grooves on a hardened steel (58 – 62 HRc) gear shaft using an Emag-Karstens machine. A 450 mm diameter wheel with a profile optimally adapted to the wear behaviour during grinding and the required finish of the radii resulted in a 45 percent increase in tool life.
In its development of GENIS wheels, Tyrolit focussed on the needs of vehicle engine and gearbox producers with a view to increasing grinding efficiency and eliminating production bottlenecks.
It came up with a new, vitrified bond that optimizes wetting of the CBN grain, even at low levels of bond content. Through careful choice of bond constituents and firing cycles, crystallisation is closely controlled to achieve porous bond structures for good chip clearance, high mechanical strength and maximum resistance to the effects of lubricants.
The resulting free-cutting, low-force grinding at high rotational speeds makes efficient use of the CBN grain, extending tool life and retaining the wheel profile for longer. It also impacts favourably on the metallurgical properties and finish of the component surface.
In a comparative test for a cam shaft manufacturer, a GENIS wheel lasted 60 percent longer than the incumbent CBN wheel when finishing the 52 HRc cam profiles at 100 m/s on a Schaudt Zeus grinder. Moreover, internal stresses in the component were significantly lower and the power drawn by the grinding spindle was reduced.
A 40 percent extension of wheel life was achieved in another application, namely grinding the main and pin bearings on a crankshaft. A 700 mm diameter GENIS wheel on a Junker Jucrank machine ground the 54 – 58 HRc features at 100 m/s. Despite the large amount of stock removal, the free-cutting CBN wheel chosen for the job increased the number of shafts ground per wheel from 4,200 to 5,900, with good process reliability.
As for all Tyrolit's industrial grinding tools, POLARIS and GENIS wheels are fitted as standard with a Wheel Memory, an embedded microchip that holds data on the grinding wheel. Information stored includes wheel specification, setting dimensions for key datums, maximum operating speed, the length of time it has been used and remaining life.
Radio frequency identification enables two-way wireless transfer of this data between the wheel and the CNC system controlling the machine on which it is being used. Set-up time is reduced, with immediate restoration of process reliability after tool change, and crash avoidance is guaranteed as each wheel has a unique indentification.
SOURCE: Tyrolit