Sliding-Head Lathe Halves Cycle Time On Rail Industry Component
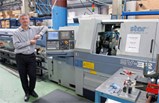
Melbourne - Since 2001, subcontractor Metaltech Precision has machined a family of six 19 mm diameter parts from Swedish iron bar on one of its 20 fixed-head lathes for a customer in the railway industry. In 2006, production volumes suddenly doubled and director Steve Hill reassessed the job, having been aware for some time that such shaft-type parts could be turned more efficiently on a sliding-headstock lathe.
He and his father John, who founded the company, were amazed at how fast these machines can be. Using an SV-32 sliding-head lathe at Star Micronics GB's Melbourne technical centre, production tests on the rail industry parts resulted in a halving of production cycle times. The saving was achieved even though only turning is required of the outside diameter, there being no prismatic element to the machining. The time saving comes from higher speed cutting on the Star and the ability of its counter spindle to face the reverse end of the component in-cycle after parting-off, saving a second set-up.
So in Autumn 2006 Steve Hill bought the SV-32, which was the first sliding-head lathe on the shop floor of 45 CNC machine tools. Star Micronics supplied a turnkey package that included a JBS compensating guide bush, which self-adjusts its pneumatic grippers continuously to allow for the relatively wide variation in the diameter of Swedish iron bar. High-pressure coolant delivery was supplied, which prolongs the life of the carbide tooling that Metaltech generally uses and allows deep holes up to 12xD to be drilled. Programs and tooling were also included in the package; and automatic fire suppression, which is now standard on all Star lathes.
Since the machine was installed at the subcontractor's factory in Chard, Somerset, it has produced all of the additional railway components during a single day shift, as well as a few short runs of other parts. A second shift has started now that Metaltech operators have become familiar with sliding-head technology, bringing the machine into line with the rest of the operation.
Having the sliding-head lathe on site soon generated new business, as Mr. Hill was able to go out and sell the capacity, knowing that the second shift was available. In July 2007, he won a major contract to mill-turn a Hitenspeed 45A carbon steel shaft for an automotive customer. Volumes were so large, however, that he decided to invest in another Star SV-32.
The second sliding-head lathe was installed in September and is now largely devoted to this contract during the day shift. Unlike the rail industry part, on which the tolerance is fairly open, the automotive component has to be machined to an 18-micron total tolerance on the OD and includes two bearing journals that require a 0.8 µm surface finish that had to be ground by the previous supplier. The part also requires driven tool work for which the nine-axis SV-32 with its live, 10-station turret is ideally suited.
Metaltech has enjoyed much success during recent years for its machined and fabricated components, which range from small turned parts to four-tonne components machined on a 6-metre bed CNC milling machine.
The company tends to specialize in difficult materials like superalloys based on nickel and titanium and / or machining complex parts in batches from 5- to 1,000-off. Two months ago the premises was extended from 30,000 to 40,000 sq ft. Number of employees has grown from 40 to 75 in the last two years and turnover this year will be £5.7 million, 35 per cent up on 2006.
SOURCE: Star Micronics GB Limited